Battery Management Systems (BMS) are at the heart of every advanced energy solution. From UAVs and robotics to EVs, marine, and defense systems. But with increasing demands for performance, safety, and compliance, how do modern BMS architectures evolve to meet these challenges?
This article summarizes the insights from our recent webinar, hosted by our very own CTO Ran Aloni, where he explored key components and architecture of BMS design, practical applications, and certification strategies. You can watch the full recording [here].
Why BMS Design Matters
A BMS is more than just a monitoring tool, it determines product safety, efficiency, customer experience, and even certification success.
Top reasons why BMS design is critical:
- Safety First: Protects against overcharge, over-discharge, short circuit, and thermal events.
- Data-Driven Insights: Enables real-time status updates, predictive maintenance, and performance tracking.
- Certification-Ready: Meets global standards (UN 38.3, IEC 62133, UL 2054) with robust architecture and proven components.
Core Components of a BMS
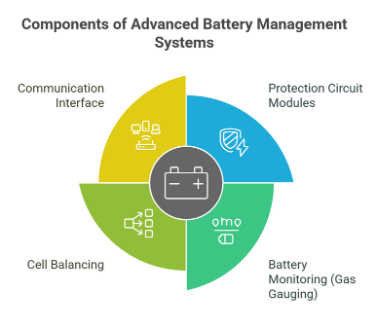
1. Protection Circuit Module (PCM)
Every BMS starts with the PCM. It’s the hardware-based guardian ensuring voltage, current, and temperature stay within safe bounds.
Common features include:
- Pack/cell over/under voltage & temperature protection
- Short circuit detection
- Pre-charge control
- Secondary protections like fuses
2. Battery Monitoring (Gas Gauging)
Two main estimation methods were discussed:
- Coulomb Counting: Measures charge in/out over time, anchored by full/empty states.
- EMF Curve Estimation: Uses voltage under 0A theoretical conditions to estimate SoC more precisely.
Together, these provide crucial insights into charge status and battery health which are essential for portable and mission-critical applications.
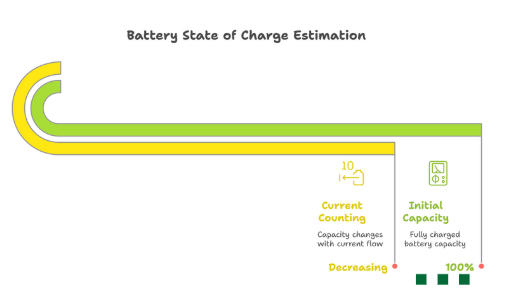
3. Cell Balancing: Passive vs. Active
Why balance? Because imbalance between cells limits usable capacity and shortens battery life.
- Passive Balancing: Bleeds excess charge from higher-voltage cells using resistors. Cost-effective and suitable for well-designed packs with premium cells.
- Active Balancing: Transfers charge from high to low cells using inductors or capacitors. Useful in large, high-capacity, or chemically imbalanced systems.
Key takeaway: In most standard applications, passive balancing suffices if the battery is built with high-quality cells and a homogenous structure.
4. Communication Interfaces
You’ve gathered the data so now how do you use it?
- Standard Protocols: SMBus (low-power I2C), UART, CAN, RS485/422
- Advanced Integration: MODBUS, CANopen, DroneCAN, TCP/IP, Bluetooth
- Key Considerations: Electromagnetic interference (EMI), standby power, and battery addressing
Tip: Always treat the battery as the slave device in communication chains to preserve energy and prevent data conflicts.
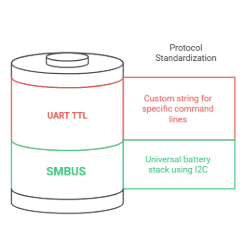
Practical Use Cases:
High Voltage Applications (EVs, UAVs, Marine)
Centralized vs. Decentralized BMS
- Centralized: All safety and monitoring in one unit efficient for compact systems.
- Decentralized: Splits functions across modules (ideal for 100–1000V batteries), reducing wire complexity and enabling module-level diagnostics.
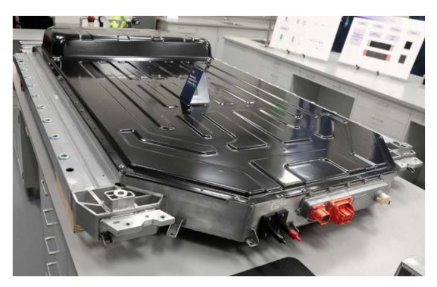
Critical Power Scenarios (Aviation, Defense)
When safety overrides may be dangerous
- No BMS: Rare, but possible in guided systems.
- Land/Air Modes: Full protection on land, limited mid-flight.
- External Discharge Protection: Fuse or smart controller outside the BMS.
Example: In a drone, an overprotective BMS that cuts power mid-air may be riskier than tolerating a temporary fault.
Certification Considerations: Build for Success from the Start
Achieving regulatory approval whether it's UN 38.3, IEC 62133, or UL 2054 is more than a checkbox. It starts with how your battery and BMS are designed. A certifiable BMS must be built from the ground up with compliance in mind:
- Fixed Configuration - Full control over the bill of materials (BOM), firmware, and hardware design.
- Multiple Safety Layers - Redundant protection mechanisms to survive single-point failures.
- Mechanical Integrity - Physically robust design with proper PCB layout, stable connectors, and secure wire routing.
- Qualified, Certified Design Team - A BMS is only as good as the engineers behind it. Your team must understand certification paths, safety protocols, and design constraints. Look for partners with:
- Proven BMS development experience
- ISO-certified processes (e.g., ISO 9001 for quality management)
- Familiarity with SIL (Safety Integrity Level) design practices
While a BMS doesn’t receive a standalone certification, its design and validation process are thoroughly assessed during battery certification. Choosing a partner with the right technical expertise and quality systems is key to avoiding costly delays or rework.
Final Thoughts
Want to explore the topic further? The full webinar recording is available here
In today’s demanding applications, BMS design is not optional but it’s strategic. From safety and performance to real-time data and compliance, a thoughtfully designed BMS unlocks product potential and ensures reliability in the field.
At Dan-Tech Energy, our engineering team brings decades of experience in power management, custom PCB design, and battery certification support. Backed by global manufacturing and ISO-compliant processes, we help customers move from concept to production with confidence.
Whether you're building a UAV powertrain, an industrial robot, or an energy storage system, the right partner can make all the difference.
-----
Ready to take your battery system to the next level? Try our intuitive ToolBox Technology to kickstart your custom battery design.
Stay informed: Subscribe to our newsletter to keep up with battery tech, case studies, and expert insights from Dan-Tech Energy.